Types of problems in the use of dispensing valves
作者:馬交易???日期:2019-08-29 15:36???瀏覽:
1. Leakage of rubber valves
Leakage problems usually occur after the dispensing valve closes. 95% of the cases occur because the needle caliber is too small to match.
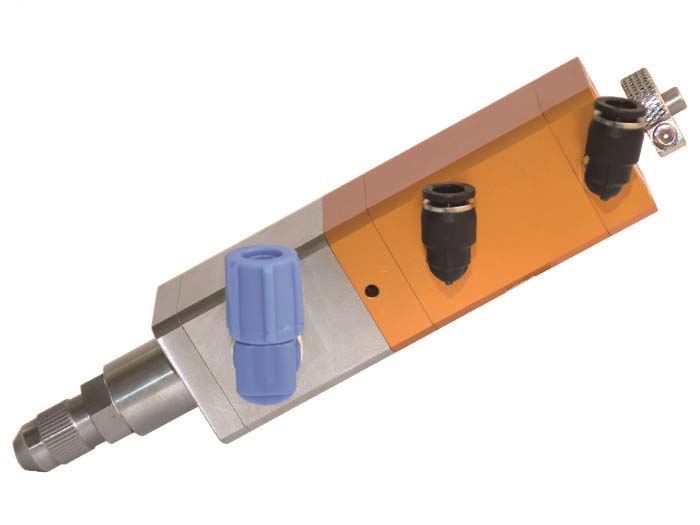
Too small a needle can affect the flow of liquid and cause back pressure. Therefore, the dispensing valve can not accept the strength of backdraft, and will soon form dripping at the rubber mouth. When the dispensing valve is used again, too small needle will affect the function of exhaust bubbles. Rubber valves can adjust the input pressure, not too high pressure, but can drive glue, but also can be fine-tuned. After adjusting the size of the dispensing needle, we began to use the specifications of the dispensing needle to solve the problem of the rubber valve, because the size of the dispensing needle will directly affect the back pressure, so we just need to replace the larger needle.
The conical oblique needle produces the lowest back pressure and the smoothest flow of liquid. When the filling valve closes, the air in the liquid leaks. It is better to remove air from the fluid in advance or to use glue which is not easy to contain bubbles, or to use glue after centrifugal stirring.
2. The size of glue is different.
When the discharge of glue flow is inconsistent, it is mainly caused by unstable pressure cylinder or uneven colloid force.
Pneumatic valves shall be set to be 10 to 15 psi lower than the factory minimum pressure. The pressure used in the pressure tube should be above the pressure in the middle of the pressure gauge, and the pressure in the low pressure part of the pressure gauge should be avoided. The pressure of dispensing controller should be at least 60 psi to ensure the stability of the glue filling. Finally, check the coating time. If less than 15/1000 seconds, the coating will be unstable, and the longer the rubber time, the more stable the amount of rubber.
3. Flow velocity is too slow
If the flow rate is too slow, the pressure can be increased or the needle can be changed within the specification range. If the hose is too long, the excess hose can also be cut appropriately.
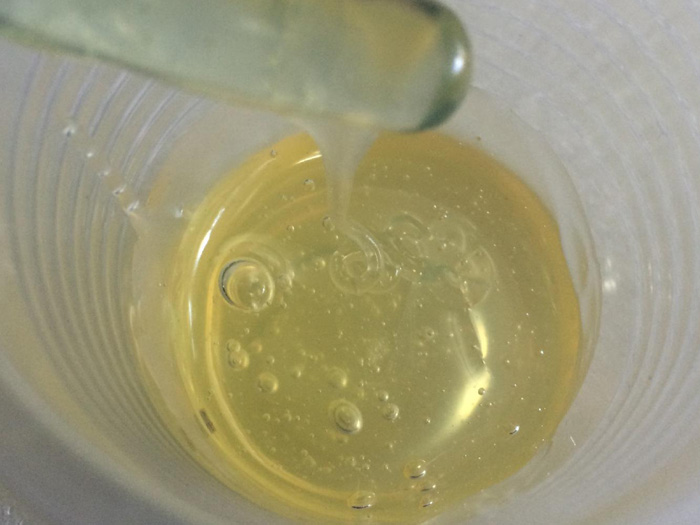
4. Bubbles in Fluid
If the valve is opened too short, excessive fluid pressure may cause air to seep into the liquid. The solution is to reduce fluid pressure and use tapered oblique needles.
5. If the joints and pipes are blocked by glue. This situation is mainly due to excessive moisture or reuse of glue, not timely cleaning led to problems.
The solution to the problem of blockage of dispensing valve: the hose is thoroughly cleaned with acetone, and there is no water. It should be determined that the air pressure used is dry, and air filters need to be installed on the air pressure valve to discharge moisture from the air.